More About Alcast Company
More About Alcast Company
Blog Article
9 Easy Facts About Alcast Company Explained
Table of ContentsSome Known Details About Alcast Company The 10-Minute Rule for Alcast CompanyUnknown Facts About Alcast CompanyThe Best Guide To Alcast CompanyAlcast Company for BeginnersThe Facts About Alcast Company Uncovered
Chemical Comparison of Cast Aluminum Alloys Silicon advertises castability by decreasing the alloy's melting temperature and enhancing fluidity during casting. In addition, silicon contributes to the alloy's strength and put on resistance, making it important in applications where durability is vital, such as vehicle components and engine parts.It additionally enhances the machinability of the alloy, making it easier to process right into ended up products. By doing this, iron adds to the total workability of light weight aluminum alloys. Copper boosts electrical conductivity, making it helpful in electrical applications. It likewise improves corrosion resistance and includes to the alloy's general stamina.
Manganese adds to the stamina of aluminum alloys and enhances workability (aluminum casting company). It is frequently utilized in functioned aluminum products like sheets, extrusions, and accounts. The existence of manganese help in the alloy's formability and resistance to breaking during construction processes. Magnesium is a light-weight aspect that provides stamina and impact resistance to light weight aluminum alloys.
More About Alcast Company
Zinc boosts the castability of aluminum alloys and assists manage the solidification process throughout casting. It improves the alloy's toughness and hardness.

The key thermal conductivity, tensile toughness, yield stamina, and prolongation differ. Among the above alloys, A356 has the highest possible thermal conductivity, and A380 and ADC12 have the most affordable.
Getting My Alcast Company To Work
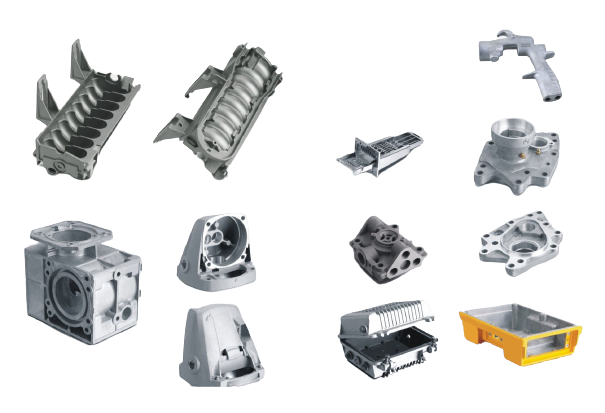
In accuracy spreading, 6063 is well-suited for applications where detailed geometries and high-grade surface coatings are paramount. Instances consist of telecommunication rooms, where the alloy's superior formability allows for sleek and visually pleasing styles while keeping architectural honesty. In the Lights Solutions industry, precision-cast 6063 components create classy and efficient illumination fixtures that need complex forms and excellent additional resources thermal efficiency.
The A360 displays remarkable elongation, making it optimal for complicated and thin-walled components. In precision spreading applications, A360 is fit for sectors such as Customer Electronics, Telecommunication, and Power Devices.
Alcast Company Things To Know Before You Get This
Its special homes make A360 a beneficial option for precision casting in these markets, boosting item durability and quality. aluminum foundry. Light weight aluminum alloy 380, or A380, is an extensively made use of spreading alloy with several distinctive attributes.
In precision spreading, light weight aluminum 413 shines in the Customer Electronic Devices and Power Tools markets. This alloy's premium deterioration resistance makes it an outstanding selection for outside applications, guaranteeing long-lasting, sturdy products in the discussed industries.
The 9-Minute Rule for Alcast Company
The aluminum alloy you select will considerably influence both the casting process and the homes of the last item. Due to the fact that of this, you should make your decision thoroughly and take an educated technique.
Determining the most suitable aluminum alloy for your application will certainly indicate considering a vast array of features. These comparative alloy qualities follow the North American Die Casting Organization's standards, and we've split them into two categories. The first category addresses alloy characteristics that affect the manufacturing procedure. The second covers attributes impacting the properties of the final item.
The Best Strategy To Use For Alcast Company
The alloy you choose for die spreading directly impacts numerous elements of the spreading process, like just how simple the alloy is to deal with and if it is prone to casting issues. Hot cracking, likewise recognized as solidification breaking, is a typical die spreading problem for light weight aluminum alloys that can cause interior or surface-level splits or splits.
Specific light weight aluminum alloys are much more at risk to hot splitting than others, and your selection must consider this. It can harm both the cast and the die, so you need to look for alloys with high anti-soldering residential properties.
Rust resistance, which is already a noteworthy feature of aluminum, can differ substantially from alloy to alloy and is a vital characteristic to consider depending upon the ecological problems your item will certainly be exposed to (Aluminum Castings). Put on resistance is an additional home frequently looked for in light weight aluminum products and can separate some alloys
Report this page